Piping Technologies
Piping technologies encompass the design, engineering, materials selection, fabrication, installation, and maintenance of pipe systems used to transport liquids, gases, and sometimes solids, from one point to another. These systems are fundamental components of a wide range of industrial, commercial, and residential infrastructure, serving as the veins and arteries through which essential fluids flow to support various processes and services.
Definition of Piping Technologies
Piping technologies involve a multidisciplinary approach to ensure the safe, efficient, and reliable transport of fluids. This includes the application of fluid mechanics, material science, structural engineering, and process engineering to design systems that meet specific operational requirements, while adhering to regulatory standards and environmental considerations. Key aspects include pipe material selection (steel, plastic, copper, etc.), size and thickness determination, pipe layout and routing, stress analysis, and the selection of appropriate fittings, valves, and other control components.
Importance in Various Industries
- Oil and Gas: In the oil and gas industry, piping systems are crucial for the extraction, transportation, and refining of crude oil and natural gas. Pipelines cover vast distances and are engineered to withstand harsh conditions, including high pressures, corrosive environments, and temperature extremes. They are integral to both upstream operations (extraction), midstream processes (transportation), and downstream activities (refining and distribution).
Pipelines Valves at gas plant - Water Treatment: Piping technologies are essential in water treatment plants for conveying raw water to the plant, and for distributing treated water to residential and commercial areas. They also play a crucial role in the various stages of treatment, including sedimentation, filtration, and chemical treatment, ensuring that water is safe for consumption and use.
- Construction: In the construction industry, piping systems are installed in buildings and facilities for water supply, heating and cooling (HVAC systems), gas distribution, and waste removal. These systems are designed to meet the specific needs of each building while ensuring safety, efficiency, and compliance with building codes and standards.
- Manufacturing: Piping systems in manufacturing plants are used for a wide array of purposes, including the supply of raw materials, the transportation of intermediate products within the plant, the delivery of compressed air or gases for various processes, and the removal of waste products. The design of these systems takes into account the specific requirements of the manufacturing process, including the need for precise control and the avoidance of contamination.
In all these industries, the reliability and safety of piping systems are paramount. Failures can lead to significant operational disruptions, environmental damage, and safety hazards. As such, piping technologies are continuously evolving, with ongoing research and development focused on improving materials, design methodologies, and maintenance practices to enhance system performance, durability, and sustainability.
Piping products are integral components of any piping system, designed to transport fluids efficiently and safely across various applications. These products can be broadly categorized into pipes, fittings, and accessories, with each category having a range of specialized solutions to meet the diverse requirements of different industries and applications. Let’s delve into each category:
Types of Pipes
Pipes can be classified based on the materials they are made from, each offering distinct advantages and suited for specific applications:
- Steel Pipes: These are widely used in high-pressure applications and environments where durability and strength are paramount, such as in the oil and gas industry. They include carbon steel pipes, which are common in industrial processes, and stainless steel pipes, known for their resistance to corrosion and heat.
- PVC (Polyvinyl Chloride) Pipes: PVC pipes are lightweight, resistant to corrosion and chemicals, making them a popular choice for residential and commercial plumbing, wastewater treatment, and irrigation systems.
- HDPE (High-Density Polyethylene) Pipes: Known for their high strength-to-density ratio, HDPE pipes are used in water and gas distribution networks, sewer systems, and in the mining industry for slurry transport. They are appreciated for their flexibility, resistance to chemicals, and ease of installation.
- Copper Pipes: Common in plumbing and HVAC systems due to their excellent thermal conductivity and resistance to corrosion. They are particularly suited for hot and cold water supply lines.
- PEX (Cross-linked Polyethylene) Pipes: PEX is used in plumbing systems for its flexibility, resistance to scale and chlorine, and ability to withstand high temperatures. It’s often used in residential water supply lines.
Fittings and Accessories
Fittings and accessories are essential for connecting pipes, changing the direction of flow, branching off, or attaching devices like valves and gauges:
- Elbows: Used to change the direction of the flow in a piping system. They come in various angles, the most common being 45° and 90°.
- Tees: T-shaped fittings that split the flow or combine flows from two different lines into one. They come in equal and reducing types.
- Flanges: These are used to connect pipes, valves, pumps, and other equipment to form a piping system. They provide easy access for cleaning, inspection, or modification.
- Valves: Integral for controlling the flow of fluids, valves come in various types including ball, gate, globe, and check valves, each designed for specific functions such as regulating flow, pressure, and direction.
Specialized Piping Solutions
Certain applications require specialized piping solutions to address unique challenges:
- Insulated Pipes: These are used to maintain the temperature of the fluids being transported, crucial in HVAC systems and industrial applications where temperature control is vital.
- Flexible Pipes: Made from materials like PEX, these pipes are used in areas where rigid pipes would be impractical due to space constraints or the need for frequent movement.
- Lined Piping Systems: These consist of a metal pipe with an inner lining of different material, often used for highly corrosive or abrasive fluids. The lining material can be rubber, PTFE, or other plastics, providing protection to the metal pipe and extending its service life.
The selection of piping products depends on various factors including the type of fluid being transported, pressure and temperature conditions, environmental factors, and the specific requirements of the application. Innovations in materials science and engineering continue to enhance the performance, safety, and sustainability of piping products, catering to the evolving needs of industries worldwide.
Services in the Piping Industry
The piping industry encompasses a broad range of services designed to ensure the efficiency, safety, and reliability of piping systems across various sectors. These services cater to the lifecycle of a piping system, from its conceptualization and design through to its installation, maintenance, and eventual repair or upgrade. Here’s a closer look at these essential services:
Consulting and Design Services
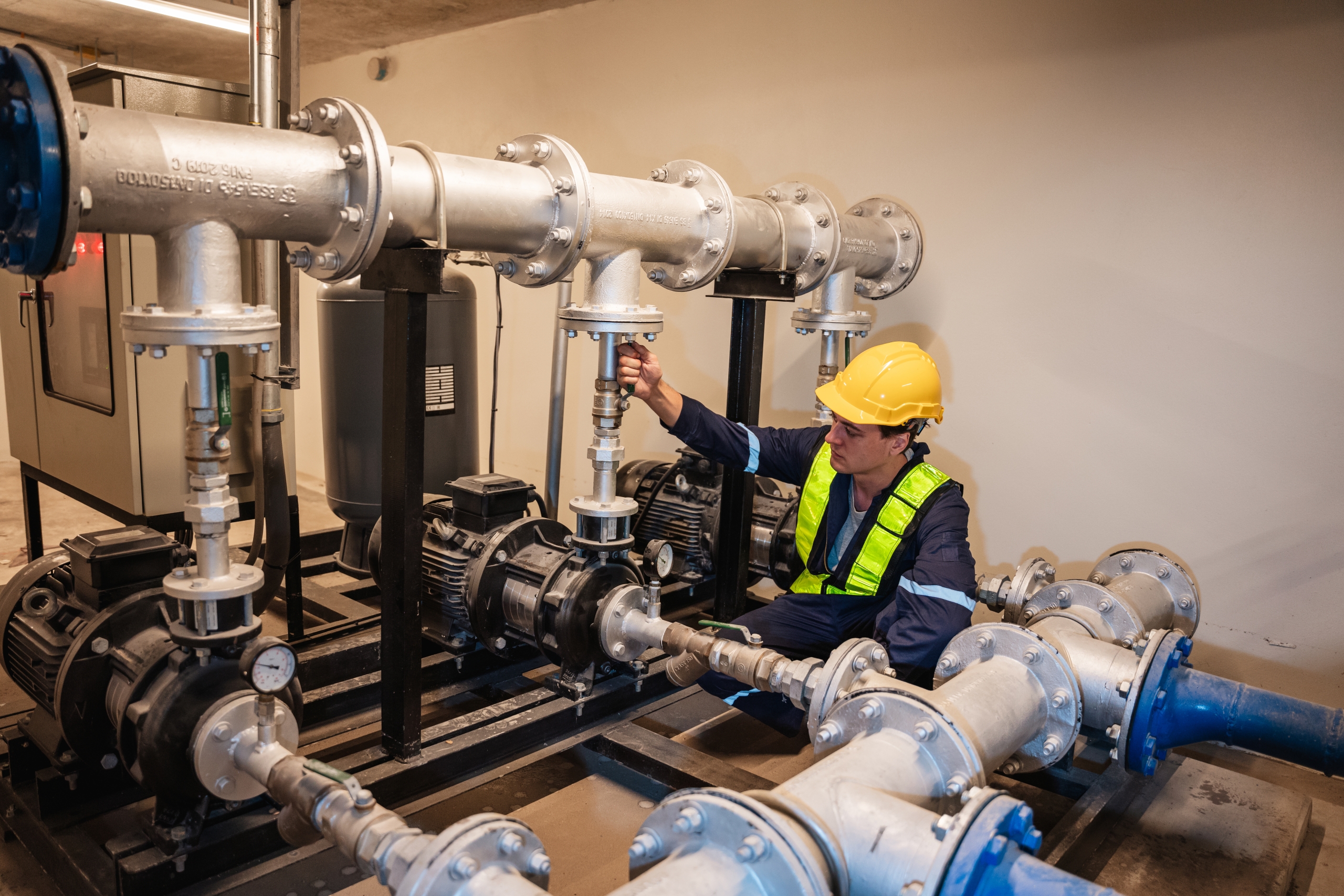
- Engineering Consultation: Specialists provide expertise in the planning and design of piping systems, offering solutions tailored to specific industry needs, regulatory compliance, and environmental considerations. This may involve feasibility studies, cost analysis, and material selection.
- Design and Modeling: Using advanced software tools like CAD (Computer-Aided Design) and CAE (Computer-Aided Engineering), professionals create detailed designs and models of piping systems. This process includes layout planning, stress analysis, and simulation to predict system behavior under various conditions.
- Project Management: Consultants offer project management services to oversee the entire piping system project from design to installation, ensuring it is completed on time, within budget, and in accordance with specifications.
Installation and Maintenance Services
- System Installation: Specialized contractors are responsible for the installation of piping systems, adhering to the detailed designs and specifications. This includes the assembly of pipes, fittings, and accessories, as well as the integration of the system into existing infrastructure when necessary.
- Preventive Maintenance: Regular maintenance services are crucial to ensure the optimal performance and longevity of piping systems. This includes routine inspections, cleaning, and the replacement of worn components to prevent failures.
- Emergency Maintenance: Providers also offer rapid response services for unexpected issues like leaks, bursts, or system malfunctions, minimizing downtime and potential damage.
Inspection and Repair Services
- Diagnostic Inspections: Advanced techniques such as ultrasonic testing, radiographic testing, and thermal imaging are used to assess the condition of piping systems and detect issues like corrosion, cracks, or leaks without dismantling the system.
- Repair Services: Depending on the issue, repairs may involve welding, patching, or the replacement of affected sections. These services aim to restore the integrity and functionality of the piping system with minimal disruption.
- Compliance Inspections: Regular inspections are conducted to ensure that piping systems comply with industry standards, safety regulations, and environmental laws. This is crucial for avoiding legal issues and ensuring the safety of operations.
Custom Fabrication Services
- Bespoke Fabrication: For unique applications or challenging environments, custom fabrication services provide tailored solutions. This involves the design and manufacture of custom pipes, fittings, and components to meet specific requirements.
- Material Specialization: Custom fabrication can involve a variety of materials, including exotic alloys for high-pressure or corrosive environments, ensuring the final product is perfectly suited to its intended application.
- Prototyping: Before full-scale production, prototypes may be created to test the design and functionality of custom-fabricated components, ensuring they meet the project’s requirements.
The comprehensive range of services in the piping industry underscores the complexity and critical nature of piping systems in modern infrastructure and industry. Expertise, precision, and ongoing innovation within these services are essential to meet the evolving demands of sectors reliant on efficient and reliable fluid transport systems.
Piping technologies are fundamental to a vast array of applications across diverse sectors, facilitating the efficient and safe transport of various fluids, including gases, liquids, and slurries. The applications can range from basic water supply systems in residential buildings to complex piping networks in high-tech industries. Below is an overview of the broad applications of piping technologies:
Industrial Applications
- Chemical Processing Plants: Piping systems in chemical plants are designed to handle a wide range of chemicals, often at high temperatures and pressures. They are made from materials resistant to corrosion and chemical attack, ensuring safe and efficient transport of raw materials, intermediates, and final products.
- Refineries: In oil and gas refineries, piping technologies are used to transport crude oil, natural gas, and refined products through various stages of processing. These systems must withstand harsh conditions, including corrosive environments and extreme temperatures, necessitating the use of durable and robust materials like stainless steel and alloy-based pipes.
Residential and Commercial Building Services
- Plumbing: Piping systems in residential and commercial buildings ensure the supply of clean water and the efficient removal of waste. Materials like PVC, copper, and PEX are commonly used for their durability, corrosion resistance, and suitability for potable water.
- HVAC (Heating, Ventilation, and Air Conditioning): Piping technologies play a crucial role in HVAC systems, transporting water, refrigerants, or steam to regulate temperature and maintain air quality in buildings. These systems require pipes that can efficiently transfer heat and withstand the pressures associated with heating and cooling processes.
Utility Services
- Water Supply: Municipal water supply systems rely on extensive networks of pipes to deliver water to residential, commercial, and industrial users. These systems use large-diameter pipes made from materials like ductile iron, HDPE, and PVC, designed for long-term durability and resistance to environmental factors.
- Gas Distribution: Natural gas distribution networks use piping systems to deliver gas from processing plants to end-users. These pipes, often made of HDPE or steel, are designed to handle high pressures and are subject to strict regulations to ensure safety and reliability.
Specialty Applications
- Cryogenics: Cryogenic piping systems are used to transport extremely cold materials, such as liquid nitrogen or liquid helium. These systems require specialized materials and insulation techniques to handle the low temperatures and prevent heat transfer.
- Hydraulic Systems: Hydraulic piping is essential in applications requiring the transmission of power through the pressurization of fluids, such as in manufacturing equipment, aircraft, and construction machinery. These systems use high-strength steel or alloy pipes capable of withstanding high pressures without deformation.
Each of these applications presents unique challenges, from the need for corrosion resistance and temperature management to the requirement for high-pressure durability. The choice of piping technologies, materials, and design principles is critical to meeting these challenges, ensuring the safety, efficiency, and longevity of the piping systems. Innovations in materials science, engineering, and fabrication techniques continue to expand the possibilities and applications of piping technologies across these diverse sectors.
Selecting the right piping technology supplier is crucial for the success of any project that involves the use of piping systems. The criteria for selection often revolve around factors that ensure reliability, compliance, and performance. Furthermore, understanding the landscape of suppliers, including global leaders and the role of local distributors and contractors, is essential for informed decision-making.
Criteria for Selecting a Supplier
- Quality: The quality of piping products is paramount, as it directly impacts the safety and longevity of the piping system. Suppliers should adhere to international quality standards and provide products that are durable, reliable, and suitable for the intended application.
- Certifications: Certifications from recognized bodies confirm that the supplier’s products and processes meet specific industry standards. Look for certifications such as ISO (International Organization for Standardization), ASTM (American Society for Testing and Materials), and ASME (American Society of Mechanical Engineers), which are indicative of compliance with global standards.
- Market Presence: A supplier’s experience and reputation in the market can be a good indicator of their reliability and the quality of their products and services. Suppliers with a long-standing presence and positive testimonials from similar industries or applications are often a safer choice.
- Product Range: A wide product range allows for more integrated solutions and the ability to meet diverse project requirements. Suppliers who offer a comprehensive range of pipes, fittings, and accessories can provide more cohesive and efficient piping systems.
- Technical Support and Services: Good suppliers provide not just products but also value-added services such as technical support, custom fabrication, and after-sales services. This support can be crucial for the successful implementation and maintenance of the piping system.
- Cost-Effectiveness: While cost should not be the primary criterion, it is undoubtedly an important factor. The goal is to find a supplier who offers competitive pricing without compromising on quality or reliability.
Leading Global Suppliers
Some of the leading global suppliers in the piping industry include:
- Tenaris: A global leader known for its production of steel pipes for the oil and gas industry, offering a wide range of seamless and welded pipes along with specialized services like pipe management and technical support.
- Wavin: A prominent supplier in the water management and plumbing systems market, Wavin is known for its innovative plastic piping systems used in residential, commercial, and municipal projects.
- Uponor: Renowned for its plumbing, indoor climate, and infrastructure solutions, Uponor specializes in PEX piping for heating, cooling, and plumbing applications, catering to both residential and commercial buildings.
- Saint-Gobain PAM: Part of the Saint-Gobain group, this company specializes in ductile iron pipe systems for water and sewage applications, offering a range of pipes, fittings, and valves designed for durability and performance.
The Role of Local Distributors and Contractors
Local distributors and contractors play a crucial role in the piping industry ecosystem. They act as intermediaries between global suppliers and end-users, providing accessibility to products and services. Local distributors often have a deep understanding of the regional market and regulatory environment, which enables them to offer tailored solutions and logistical support. They may also provide additional services such as inventory management, local delivery, and technical support.
Contractors, on the other hand, are responsible for the installation and maintenance of piping systems. They rely on suppliers and distributors for the provision of high-quality materials and may also offer design and engineering services to ensure that the installed systems meet the project’s specifications and regulatory requirements.
The synergy between suppliers, distributors, and contractors is vital for the smooth execution of projects, ensuring that the right products are available at the right time and are installed correctly to create efficient, reliable, and compliant piping systems.
Codes, standards, and regulations play a crucial role in the piping industry by ensuring safety, reliability, and efficiency in the design, fabrication, installation, and maintenance of piping systems. These guidelines provide a framework for industry professionals to adhere to, ensuring that piping systems meet the required quality and safety benchmarks.
Significance of Codes and Standards
- Safety: They ensure the safety of personnel, the public, and the environment by minimizing the risk of accidents and leaks, which can lead to catastrophic outcomes.
- Reliability: Adherence to established codes and standards enhances the reliability of piping systems, ensuring they perform effectively under the designated conditions.
- Interoperability: Standards facilitate compatibility and interoperability between equipment and components from different manufacturers, promoting efficiency and ease of maintenance.
- Regulatory Compliance: In many jurisdictions, complying with relevant codes and standards is a legal requirement. Non-compliance can result in penalties, legal action, and the invalidation of insurance policies.
- Quality Assurance: They provide a benchmark for quality, helping manufacturers and service providers maintain consistent product and service quality.
Overview of Major International Standards
- ASME (American Society of Mechanical Engineers): ASME’s B31 series is among the most widely used standards for piping systems design, fabrication, inspection, and testing. The B31.1 code, for example, covers power piping, while B31.3 is focused on process piping used in petrochemical plants.
- ASTM (American Society for Testing and Materials): ASTM provides a wide range of standards that cover the materials used in piping systems, testing procedures, and the specifications for various piping components. These standards are critical for ensuring the materials used are appropriate for their intended applications.
- ISO (International Organization for Standardization): ISO offers international standards that ensure quality, safety, and efficiency across various industries worldwide. ISO standards relevant to piping include those related to dimensions, material quality, and testing methods.
National and Local Regulations Impacting Piping Technologies
In addition to international standards, national and local regulations can have a significant impact on piping technologies:
- National Codes and Standards: Countries may have their own specific codes and standards that supplement or deviate from international standards. For example, the UK uses BS (British Standards), and Germany uses DIN (Deutsches Institut für Normung) standards.
- Local Building Codes: Local jurisdictions may have building codes that provide additional requirements for piping systems, particularly in terms of installation practices, safety measures, and inspections. These codes ensure that systems are suited to the local environment, including considerations for climate, seismic activity, and other regional factors.
- Environmental Regulations: Environmental regulations at both the national and local levels can impact the design and operation of piping systems. These regulations might address issues such as emissions, waste management, and the use of hazardous materials.
- Health and Safety Regulations: Regulations focused on health and safety can dictate specific requirements for piping systems, especially those carrying hazardous or toxic substances. They aim to protect workers and the public from potential exposure to dangerous materials.
Navigating the complex landscape of codes, standards, and regulations requires a thorough understanding and ongoing vigilance, as these guidelines are subject to updates and revisions. Compliance not only ensures legal and regulatory adherence but also underscores a commitment to safety, quality, and environmental stewardship in the piping industry.
Innovations and Trends in Piping Technologies
The piping industry is witnessing significant innovations and trends, driven by advancements in technology, growing environmental concerns, and the increasing demands of modern infrastructure. These innovations are transforming the way piping systems are designed, manufactured, installed, and maintained.
Advancements in Materials and Manufacturing Processes
- New Material Technologies: The development of new materials such as high-performance polymers, composites, and corrosion-resistant alloys offers improved durability, efficiency, and longevity for piping systems. These materials can withstand harsh chemicals, high temperatures, and extreme pressures, expanding the applications of piping systems.
- Additive Manufacturing (3D Printing): 3D printing is revolutionizing the manufacturing of piping components, allowing for the creation of complex shapes and geometries that were previously difficult or impossible to achieve. This technology enables rapid prototyping, customization, and on-demand production, reducing lead times and costs.
- Enhanced Coating Techniques: Advanced coating technologies are being developed to enhance the protective properties of pipes, improving their resistance to corrosion, abrasion, and UV radiation. These coatings extend the life of piping systems and reduce the need for maintenance.
The Rise of Smart Piping Systems and IoT Integration
- Sensor Integration: The integration of sensors into piping systems enables real-time monitoring of pressure, temperature, flow rates, and other critical parameters. This data can be used to optimize system performance, predict maintenance needs, and prevent failures.
- IoT (Internet of Things) Connectivity: IoT-enabled piping systems can communicate with other systems and devices, facilitating automated control, remote monitoring, and data analysis. This connectivity allows for more efficient operations, improved safety, and reduced downtime.
- Predictive Maintenance: Leveraging data analytics and machine learning, smart piping systems can predict potential issues before they lead to system failures. This proactive approach to maintenance helps avoid costly repairs and extends the lifespan of the system.
Sustainability Trends: Recycling, Energy Efficiency, and Reduced Environmental Impact
- Recycled and Renewable Materials: There is a growing trend towards using recycled materials in the manufacturing of pipes and fittings, reducing the environmental impact and promoting circular economy principles. Some companies are also exploring the use of bio-based plastics and composites.
- Energy-Efficient Design: Energy efficiency is becoming a key consideration in the design of piping systems. Innovations such as improved insulation materials, energy recovery systems, and optimized system layouts contribute to reducing energy consumption.
- Reduced Environmental Footprint: The industry is focusing on minimizing the environmental footprint of piping systems through the entire lifecycle, from manufacturing and installation to operation and decommissioning. This includes reducing water usage, minimizing waste, and implementing sustainable practices in sourcing and production.
These innovations and trends reflect the piping industry’s response to the evolving demands of infrastructure development, environmental sustainability, and technological advancement. As the industry continues to innovate, we can expect to see smarter, more sustainable, and more efficient piping systems that meet the needs of the future.
Challenges and Solutions in Piping Technologies
Piping technologies, while integral to various industrial and infrastructure systems, face a range of challenges that can impact their efficiency, safety, and longevity. Addressing these challenges requires ongoing research, innovation, and the adoption of best practices.
Addressing Corrosion, Scaling, and Material Compatibility
- Corrosion and Scaling: Corrosion and scaling can significantly reduce the lifespan and efficiency of piping systems. Solutions include the use of corrosion-resistant materials (such as certain alloys, composites, and non-metallic materials), protective coatings, and cathodic protection systems. Additionally, water treatment and conditioning can mitigate scaling and corrosion by controlling the pH, hardness, and chemical composition of the fluids in the system.
- Material Compatibility: Selecting materials that are compatible with the fluids being transported and the environmental conditions is crucial. This requires a thorough understanding of the chemical and physical properties of materials and fluids. Advanced simulation and modeling tools can predict interactions between materials and fluids, aiding in material selection.
Ensuring Safety in High-Pressure and High-Temperature Environments
- Design and Engineering: Proper design and engineering practices are critical in high-pressure and high-temperature applications. This includes adhering to relevant codes and standards, performing rigorous stress analysis, and implementing safety factors in the design phase.
- Material Selection: Materials that can withstand extreme conditions without degrading are essential. This may involve using special alloys, composites, and ceramics designed for high-performance applications.
- Safety Devices and Systems: The integration of safety devices such as pressure relief valves, burst discs, and automatic shut-off systems can prevent catastrophic failures. Regular safety drills and training for personnel are also crucial for maintaining a safe operating environment.
Innovations in Leak Detection and Prevention
- Advanced Monitoring Technologies: Technologies such as acoustic emission sensors, infrared thermography, and fiber optic sensors can detect leaks early by monitoring changes in sound, temperature, or light transmission. These technologies enable rapid response to prevent significant losses or damages.
- Smart Piping Systems: IoT-enabled piping systems can continuously monitor the integrity of the piping network and alert operators to potential leaks or weaknesses. Machine learning algorithms can analyze historical data to predict and prevent failures.
- Improved Joint and Connection Technologies: Advances in joint and connection technologies, such as non-welded connections, mechanical joining methods, and improved sealing materials, reduce the risk of leaks. These technologies offer more reliable and durable connections, particularly in applications where welding may be impractical or undesirable.
- Preventive Maintenance and Inspection Programs: Regular inspections and maintenance are essential for leak prevention. Techniques such as ultrasonic testing, radiographic imaging, and magnetic flux leakage can identify potential issues before they result in leaks.
Addressing these challenges requires a multi-faceted approach that combines advanced materials, innovative technologies, and rigorous engineering practices. As the industry evolves, continuous improvement in design, monitoring, and maintenance practices will be essential to enhancing the safety, efficiency, and sustainability of piping systems.
Frequently Asked Questions (Q&A)
Here’s a compilation of frequently asked questions (FAQs) related to piping technologies, along with expert answers to provide insight into various aspects such as materials selection, maintenance, regulatory compliance, and more.
Q1: How do I choose the right material for my piping system?
A1: Selecting the right material depends on several factors, including the type of fluid being transported (corrosive, abrasive, temperature), pressure and temperature conditions, environmental factors, and cost considerations. Common materials include steel for high-pressure applications, PVC and HDPE for water and sewage, and copper for heating and cooling systems. It’s crucial to consider the compatibility of the material with the fluid and environmental conditions to ensure longevity and performance.
Q2: What are the key maintenance tips for ensuring the longevity of a piping system?
A2: Regular inspections and maintenance are essential. Look for signs of wear, corrosion, or leaks. Implement routine cleaning to prevent blockages and scaling. Ensure that protective coatings and insulation are intact. Use proper supports and allowances for thermal expansion to prevent stress on the system. Lastly, adhere to the manufacturer’s and industry’s maintenance guidelines.
Q3: How can I ensure my piping system complies with regulatory standards?
A3: Familiarize yourself with relevant local, national, and international codes and standards applicable to your industry and region. These might include ASME, ASTM, ISO, and specific local building codes. Engage with certified professionals for design, installation, and inspection, and ensure all materials and components are certified as per required standards. Regular audits and compliance checks can also help maintain adherence to these standards.
Q4: What are the environmental considerations in modern piping systems?
A4: Modern piping systems consider environmental impact through the use of sustainable materials, energy-efficient designs, and minimizing water usage. Recycling and using eco-friendly materials like bio-based plastics or recycled metals are becoming more common. Leak detection and prevention are also critical to prevent environmental contamination.
Q5: How do smart piping systems enhance operational efficiency?
A5: Smart piping systems use sensors and IoT technology to monitor system performance in real-time, including pressure, flow rate, and temperature. This data can be used for predictive maintenance, identifying potential issues before they lead to system failure, and for optimizing system performance, leading to improved efficiency and reduced operational costs.
Q6: Can piping systems be used for energy recovery?
A6: Yes, energy recovery systems can be integrated into piping systems, especially in industrial applications. For example, heat exchangers can recover thermal energy from hot fluid waste streams, using it to preheat incoming cold streams, thereby reducing energy consumption.
Q7: What advancements are being made in leak detection technologies?
A7: Advancements in leak detection include the use of acoustic sensors that listen for the sound of escaping fluids, fiber optic cables that detect temperature changes associated with leaks, and drone technology for inspecting hard-to-reach areas. Machine learning algorithms are also being employed to analyze data and predict potential leak points more accurately.
Q8: How do high-temperature and high-pressure conditions affect piping system design?
A8: High-temperature and high-pressure conditions require special design considerations to ensure safety and reliability. This includes selecting materials that can withstand these conditions, using thicker pipe walls or special alloys, incorporating expansion joints to accommodate thermal expansion, and implementing rigorous stress analysis during the design phase to ensure structural integrity.
By addressing these FAQs, we aim to provide a clearer understanding of the complexities and considerations involved in the design, operation, and maintenance of piping systems, catering to professionals and enthusiasts alike within the field.
Conclusion
The exploration of piping technologies reveals their indispensable role in modern industrial and civil infrastructure. Key takeaways from this discussion highlight the complexity, versatility, and evolving nature of piping systems, underlining their critical function in ensuring efficient, safe, and sustainable fluid transport across various sectors.
- Versatility and Application: Piping technologies cater to a broad spectrum of applications, from essential utilities like water and gas distribution to complex industrial processes in the oil, gas, chemical, and manufacturing sectors. Their adaptability to residential, commercial, and industrial needs underscores their universal importance.
- Material and Design Innovations: Continuous advancements in materials science and design methodologies are enhancing the performance, durability, and environmental compatibility of piping systems. The adoption of new materials like high-performance polymers and composites, alongside traditional materials like steel and copper, is expanding the capabilities of piping systems to meet diverse operational demands.
- Smart Technologies and Sustainability: The integration of smart technologies and IoT connectivity is revolutionizing the monitoring, maintenance, and operation of piping systems, paving the way for predictive maintenance and improved efficiency. Concurrently, a growing emphasis on sustainability is driving the adoption of eco-friendly materials, energy-efficient designs, and practices that reduce environmental impact.
- Regulatory and Safety Considerations: Adherence to international and local codes, standards, and regulations ensures the safety, reliability, and quality of piping systems. This regulatory framework is essential for mitigating risks and ensuring the longevity of piping infrastructures.
Future Outlook:
The future of piping technologies is intrinsically linked to the advancement of industrial and civil infrastructure. As demands for efficiency, safety, and sustainability intensify, the industry is set to witness further innovations:
- Advanced Material Development: Ongoing research into materials that offer superior strength, flexibility, and environmental resistance will continue to push the boundaries of what piping systems can achieve, particularly in challenging operational environments.
- Expansion of Smart Piping Systems: The proliferation of sensors, IoT, and AI technologies will enhance the capabilities of smart piping systems, offering unprecedented levels of operational insight, predictive maintenance, and system optimization.
- Sustainability and Circular Economy: The drive towards sustainability will intensify, focusing on the recyclability of materials, reduction of water and energy consumption, and minimization of the environmental footprint of piping systems throughout their lifecycle.
- Customization and Flexibility: As projects and applications become more complex, the ability to provide customized and flexible piping solutions will be paramount. This includes adaptive designs, modular systems, and on-demand manufacturing techniques like 3D printing.
In conclusion, the evolution of piping technologies is set to continue at pace, driven by the dual imperatives of technological innovation and sustainable development. Their role in supporting and advancing modern infrastructure, while adapting to the challenges of the 21st century, will remain invaluable, shaping the future of industrial processes, urban development, and environmental stewardship.