What Is Super Duplex Material? Composition and Properties of Super Duplex Stainless Steels
Contents
- 1 What Is Super Duplex Material?
- 2 Types of Super Duplex Stainless Steels
- 3 Composition and Properties of Super Duplex Stainless Steels
- 4 Manufacturing Processes of Super Duplex Stainless Steels
- 5 Applications of Super Duplex Stainless Steels
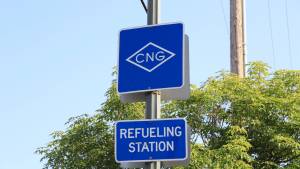
Contents1 What is a Compressed Natural Gas (CNG) station ?1.1 Introduction to Compressed Natural Gas (CNG) Stations1.2 The Rise of CNG Stations1.2.1 Environmental Incentives1.2.2 Economic Benefits1.2.3 Technological Advancements2 How CNG Stations Work2.0.1 Overview of the CNG Station Infrastructure2.0.2 The Process of Compressing Natural Gas2.0.3 Storage and Dispensing Systems at CNG Stations2.0.4 Safety Measures and Standards3 […]
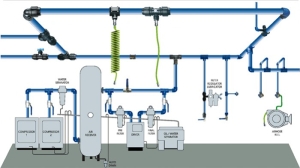
Contents1 What is Instrument Air System ?1.1 Definition and Purpose2 Components of Instrument Air Systems2.0.1 Compressors2.0.2 Air Dryers2.0.3 Filters2.0.4 Aftercoolers and Receivers2.0.5 Regulators and Distribution Systems3 Working Principle of Instrument Air Systems3.0.1 Air Compression Process3.0.2 Cooling and Moisture Separation3.0.3 Moisture Removal and Air Drying3.0.4 Filtration for Purity3.0.5 Pressure Regulation and Distribution4 Instrument air system calculations4.1 […]
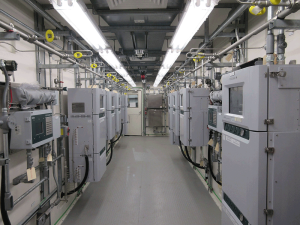
Contents1 What is a sampling system ?2 Components of sampling system3 Online and Offline sampling system3.1 Online Sampling System3.2 Offline Sampling System4 Sampling Systems for Gas and Liquide4.1 Gas Sampling Systems4.2 Liquid Sampling Systems4.3 Considerations for Both Systems5 Table to compare online and offline sampling systems6 Applications of Sampling system6.1 1. Chemical and Petrochemical Industry6.2 […]
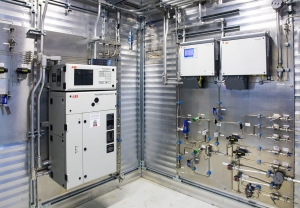
Contents1 I. What is a Sampling systems in process analyzer?1.1 Key Functions of a Sampling System1.2 Components of a Sampling System1.3 Considerations for Effective Sampling Systems1.4 Considerations for Designing Online Sampling Systems1.5 Benefits of Online Sampling Systems2 II. Key Components of Online Sampling System3 1. Fast loop in sampling system3.1 Function and Purpose3.2 Components of […]
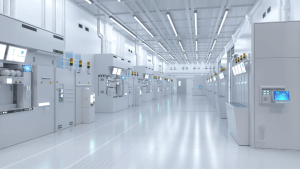
Contents1 What is clean room?2 Fundamentals of Clean Rooms3 Types of Clean Rooms3.1 US FED STD 209E Cleanroom Standards and Cleanroom Classifications3.2 FED STD 209E Cleanroom Standards3.2.1 Cleanroom Classifications3.3 ISO 14644-1 Cleanroom Standards and Cleanroom Classifications3.3.1 ISO 14644-1 Cleanroom Standards3.3.2 Cleanroom Classifications4 Design Requirements for Cleanroom Classifications4.1 1. Air Filtration and Ventilation4.2 2. Room Pressure4.3 […]

Contents1 What is Wellhead Control Panel (WHCP)?2 Understanding Well Head Control Panels (WHCP)3 Principle of Wellhead Control Panel (WHCP) Operation3.1 Main Functions of Wellhead Control Panel (WHCP)3.2 Components of Wellhead Control Panel (WHCP)4 Types of WHCP4.1 Single Wellhead Control Panels4.2 Multi-Wellhead Control Panels5 Design Wellhead Control Panel (WHCP) Considerations6 Codes and Standards compliance of Wellhead […]
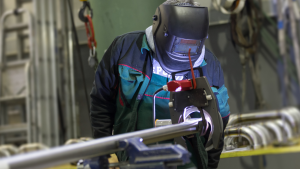
Contents1 What is orbital welding?2 Orbital welding Equipment2.1 Facing tubing machine2.2 Key aspects of facing tubing include:2.3 Tools and Equipment:2.4 Importance:2.5 10 Purge gas panel in orbital welding2.6 Components and Functions:2.7 Importance:3 Orbital welding technique3.1 Key Techniques in Orbital Welding:3.2 Advantages of Orbital Welding:4 How welding joint finished in orbital welding4.1 1. […]
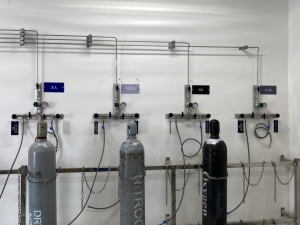
Contents1 What is a gas distribution system ?2 Gas Cylinders or Tanks2.1 Characteristics of Gas Cylinders or Tanks:2.2 Types of Gases Stored:2.3 Handling and Safety:2.4 Identification:3 Source Inlet (SSI)3.1 Features of a Source Inlet (SSI):3.2 Functions of a Source Inlet (SSI):3.3 Applications:3.4 Maintenance and Operation:4 Primary Gas Panels Control4.1 Single-Stage Gas Panel (SGP)4.2 Dual-Stage Gas […]
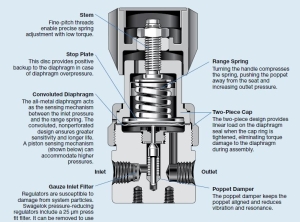
A pressure regulator is a device used to control and maintain a desired pressure level in a system. It is commonly used in various industrial and commercial applications where precise pressure control is necessary. The basic function of a pressure regulator is to reduce the input pressure to a lower, predetermined pressure level, […]