What is a fusible plug? How does it work?
Contents
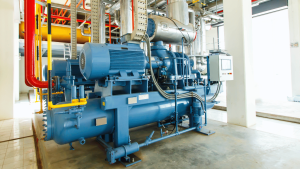
Contents1 What is centrifugal pump?1.1 Introduction to Centrifugal Pumps1.1.1 Definition and Basic Principle1.1.2 Historical Development1.1.3 Common Applications2 Components and Design of Centrifugal Pumps2.1 Impeller Design and Types2.2 Casing Types2.3 Shaft, Bearings, and Seals2.4 Suction and Discharge Parts3 Operating Principles of Centrifugal Pumps3.0.1 The Physics Behind Centrifugal Action3.0.2 Fluid Dynamics in the Pump3.0.3 The Role of […]
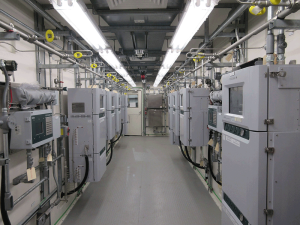
Contents1 What is a sampling system ?2 Components of sampling system3 Online and Offline sampling system3.1 Online Sampling System3.2 Offline Sampling System4 Sampling Systems for Gas and Liquide4.1 Gas Sampling Systems4.2 Liquid Sampling Systems4.3 Considerations for Both Systems5 Table to compare online and offline sampling systems6 Applications of Sampling system6.1 1. Chemical and Petrochemical Industry6.2 […]
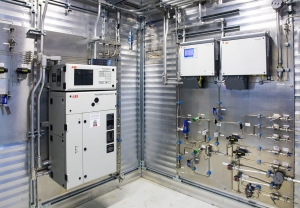
Contents1 I. What is a Sampling systems in process analyzer?1.1 Key Functions of a Sampling System1.2 Components of a Sampling System1.3 Considerations for Effective Sampling Systems1.4 Considerations for Designing Online Sampling Systems1.5 Benefits of Online Sampling Systems2 II. Key Components of Online Sampling System3 1. Fast loop in sampling system3.1 Function and Purpose3.2 Components of […]
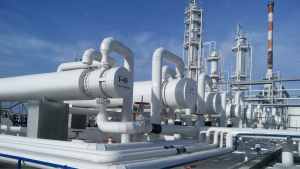
Contents1 What is a heat exchanger?2 Types of Heat Exchangers2.1 Shell and Tube Heat Exchangers2.2 Plate and Frame Heat Exchangers2.3 Air Cooled Heat Exchangers2.4 Condensers and Evaporators Heat Exchangers2.5 Specialty Heat Exchangers3 Components of heat exchanger3.1 1. Tubes or Plates3.2 2. Shell3.3 3. Flow Configuration3.4 4. Inlet and Outlet Ports3.5 5. Baffles3.6 6. End Caps […]
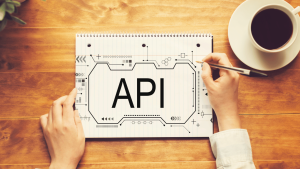
Contents1 What is API standards of piping ?2 List of API standards of piping engineer3 API standards for offshore structure4 API standards for Valves and Wellhead Equipment5 API standards for Production Equipment6 The American Petroleum Institute (API) for Pipeline Operation7 The American Petroleum Institute (API) for Storage Tank Safety8 API standards petroleum standards8.1 Exploration and Drilling8.2 […]
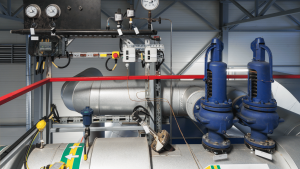
Contents1 Introduction Overview of boiler systems and boiler pressure relief valves (PRVs)1.1 Definition of a Boiler Pressure Relief Valve1.2 Function of a Boiler Pressure Relief Valve1.3 Prevention of Overpressure Conditions2 The Need for Pressure Relief in Boilers2.1 How Pressure Builds Up in a Boiler System2.2 Potential Risks Associated with Excessive Pressure3 Components of a Boiler […]

Contents1 What is pressure relief valve ?2 Components of pressure relief valve3 Pressure relief valve symbol4 How does pressure relief valve work?5 How to calculate flow of relief valve5.1 1. Determine Fluid Properties5.2 2. Valve Specifications5.3 3. Set Pressure and Back Pressure5.4 4. Calculate Flow Capacity5.5 For Gases and Vapors (Including Steam)5.6 For Liquids5.7 5. […]

Contents1 What is pressure transmitter ?2 What are the components of a pressure transmitter?3 Working Principle of pressure transmitter4 Types of pressure transmitters4.1 Advance and Disadvantage of each types of pressure transmitter4.2 Absolute Pressure Transmitters4.3 Gauge Pressure Transmitters4.4 Differential Pressure Transmitters4.5 Sealed Gauge Pressure Transmitters4.6 Multivariable Transmitters4.7 Capacitive Pressure Transmitters4.8 Piezoelectric Pressure Transmitters4.9 Strain Gauge […]
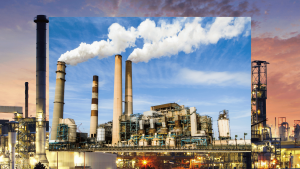
Contents1 What are petrochemicals?2 Overview outline of what are petrochemicals plant3 Petrochemicals plant technologies4 The products of petrochemical factory4.1 Primary Petrochemicals4.2 Secondary Petrochemicals4.3 Specialty Chemicals and Products5 Petrochemical Processing – From Raw Material to Final Usage5.1 1. Extraction of Raw Materials5.2 2. Separation and Refinement5.3 3. Primary Petrochemical Production5.4 4. Intermediate Chemicals Production5.5 5. Specialty […]